
Tariff policies are redefining the global supply chain for power tools, altering costs, sourcing, and production strategies. Recent trade reports reveal that over 30% of firms now view tariffs as their top business concern, with more than half planning to diversify supply chains. Companies like Weida and Dechang are adapting by establishing operations in emerging markets. Meanwhile, component manufacturers such as HuaJie, Szhittech, and Topband are shifting focus to regions like Southeast Asia and Mexico, leveraging competitive advantages to mitigate rising costs and delays.
Key Takeaways
- Tariff rules are changing how power tools are made and sold.
- Costs are rising, so companies are rethinking where they get materials.
- Over 30% of businesses now see tariffs as a big problem.
- Many are using more suppliers to avoid risks from tariffs.
- Southeast Asia, like Vietnam and Thailand, is a popular place to make tools.
- These countries have cheaper workers and good trade deals.
- Mexico is close to the U.S., saving on shipping and avoiding tariffs.
- Companies are building factories in new places to handle tariff issues.
- The power tools industry is focusing more on being eco-friendly.
- Manufacturers are using green methods because customers want them.
- Automation and technology are making supply chains faster and cheaper.
- Companies are working with local suppliers to handle trade changes better.
Overview of Tariff Policies
Recent Tariff Changes

U.S. tariffs on Chinese imports
The United States has implemented significant tariff increases on Chinese imports in recent years. These measures, introduced during the U.S.-China trade war, aimed to protect domestic industries and reduce trade deficits. However, they have also disrupted global trade dynamics. Many power tools, including drills, saws, and grinders, now face higher import duties, making them more expensive for U.S. consumers and businesses. This shift has forced manufacturers to reevaluate their supply chains and explore alternative production locations.
Key power tools products affected
The tariff hikes have particularly impacted electric power tools and their components. Products such as cordless drills, angle grinders, and battery packs have seen increased costs due to higher import duties. These changes have not only affected pricing but also influenced sourcing strategies. Manufacturers are now prioritizing regions with lower tariffs and production costs to maintain competitiveness in the global market.
Global Trade Implications
Rising trade tensions and their effects
Rising trade tensions between major economies have created uncertainty in global markets. The U.S.-China trade war, for instance, has led to a 34% increase in firm exits from China. This exodus highlights how political risks and tariffs can significantly alter manufacturing landscapes. Since 2019, the number of new trade restrictions has tripled, further escalating geopolitical risks. These developments have disrupted long-standing trade relationships and increased the complexity of global supply chains.
Shifts in global trade and manufacturing costs
The evolution of tariff policies has reversed decades of progress toward tariff liberalization. Historical data illustrates this trend. For example:
Year | Average Tariff Rate |
---|---|
1790 | 20% |
1860 | 15% |
1934 | 5% |
1942 | 13.4% |
2016 | Increased due to protectionism |
The recent tariff increases have driven up manufacturing costs, compelling businesses to adapt. Many companies have shifted production to regions like Southeast Asia and Mexico, where lower tariffs and competitive labor costs offer a more favorable environment. These changes underscore the need for businesses to remain agile in response to evolving trade policies.
Shift of Complete Electric Power Tool Manufacturers
The vast majority of manufacturers have established factories in Southeast Asia or Mexico.
The global power tools industry has witnessed a significant relocation of manufacturing facilities. Many companies have shifted their production bases to Southeast Asia and Mexico to counteract rising tariffs and operational costs. This strategic move has allowed manufacturers to maintain competitive pricing while accessing skilled labor and favorable trade agreements.
The country preferences, in order, are Vietnam, Thailand, and Mexico.
Vietnam has emerged as the top choice for manufacturers. Its proximity to major shipping routes, competitive labor costs, and participation in multiple free trade agreements make it an attractive destination. The Vietnamese government has also introduced policies to encourage foreign investment, further solidifying its position as a manufacturing hub.
Thailand follows closely, offering a robust infrastructure and a well-established industrial base. The country’s strategic location within Southeast Asia provides easy access to regional markets. Additionally, Thailand’s skilled workforce and government incentives for manufacturing industries have drawn significant attention from global power tool manufacturers.
Mexico ranks third but remains a critical player due to its geographical advantage. Its proximity to the United States, the largest market for power tools, reduces transportation costs and delivery times. The United States-Mexico-Canada Agreement (USMCA) has further enhanced Mexico’s appeal by providing tariff-free access to North American markets. However, challenges such as scaling production and infrastructure limitations persist.
Note: The shift to these regions reflects a broader trend of decentralizing manufacturing to mitigate risks associated with tariffs and geopolitical tensions. This strategy not only diversifies supply chains but also ensures resilience in a rapidly changing global trade environment.
Manufacturers are leveraging these relocations to optimize production efficiency and reduce dependency on traditional manufacturing hubs. This transition marks a pivotal moment in the power tools industry, reshaping its global supply chain dynamics.
Shift of Component Manufacturers
The relocation of component manufacturers has become a critical aspect of the global power tools supply chain transformation. As complete electric power tool production shifts to Southeast Asia and Mexico, key component suppliers are following suit. This strategic move ensures seamless integration into new manufacturing hubs while addressing tariff challenges and operational costs.
Battery Cell Manufacturers

TENPOWER 天鹏电源

TENPOWER, a leading Chinese battery cell manufacturer, has accelerated its global expansion in response to evolving tariff policies. The company recently initiated its first overseas project in Selangor, Malaysia, with a total investment of approximately $280 million. This facility, dedicated to producing 10GWh cylindrical lithium batteries, began construction in November 2023 and reached its structural completion by June 2024.

The first phase of the project is expected to commence operations by the second quarter of 2025, with an annual production capacity exceeding 400 million units. The product lineup includes mainstream high-rate and high-capacity cells, along with a new production line for all-tab batteries. This expansion strengthens TENPOWER’s ability to support global high-end clients in the power tools sector and enhances its competitiveness in Southeast Asia and South Asia. The Malaysian facility positions the company to cater to emerging markets, including two-wheeler manufacturers, while bolstering its global service capabilities.


Electronic Control Manufacturers
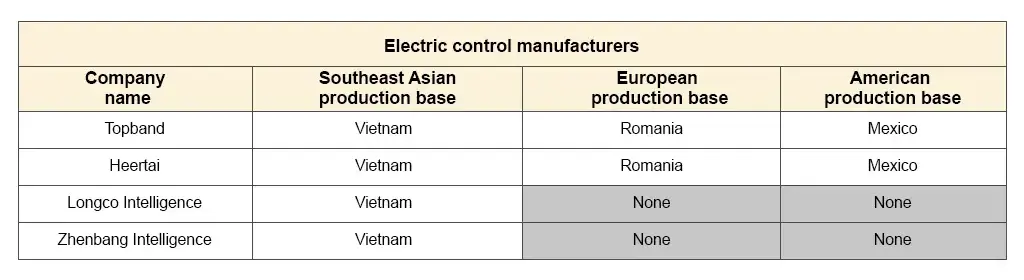
Topband 拓邦
Topband, established in 1996 and listed on the Shenzhen Stock Exchange in 2007, specializes in intelligent control system solutions. Its core technologies, known as the “Four Electrics and One Network,” encompass electronic controls, motors, batteries, power supplies, and IoT platforms. These solutions serve industries such as home appliances, tools, renewable energy, and industrial automation. In 2023, Topband reported revenue of $12.3 billion, reflecting its robust market presence.
szhittech 和而泰
Szhittech, a global leader in smart controllers for home appliances and power tools, has strategically expanded its manufacturing footprint. The company operates facilities in Vietnam, Mexico, and Romania. Its Vietnam factory achieved profitability within months of operation, showcasing its cost-efficiency. The Mexican facility, set to launch in 2024, aims to serve the North American market more effectively. This strategic positioning allows Szhittech to meet local demand while optimizing production costs.
Switch Manufacturers

huajie 华之杰
Founded in 1992, Huajie specializes in the development and production of switches, sockets, connectors, and electronic modules. The company’s UL-certified laboratory underscores its commitment to quality and innovation. Recognized as a Foreign Investment R&D Center in Jiangsu Province, Huajie continues to lead in switch manufacturing. Its advanced capabilities and adherence to international standards make it a key player in the global power tools supply chain.
Note: The relocation of component manufacturers highlights the industry’s adaptability to changing trade dynamics. By establishing operations in emerging markets, these companies ensure resilience and competitiveness in a rapidly evolving global landscape.
Motor Manufacturers

Dechang-motor 德昌股份
Dechang-motor, a prominent player in the motor manufacturing industry, has established itself as a key supplier for global power tool brands. The company specializes in the development and production of motors for household appliances and power tools. Its product portfolio includes motors for vacuum cleaners, humidifiers, hair dryers, and electric fans. This diverse range highlights its adaptability and technical expertise.
In recent years, Dechang-motor has expanded its presence in the international market. By 2023, it became a supplier for major brands such as Techtronic Industries (TTI), Helen of Troy (HOT), and Shark. These partnerships have solidified its reputation as a reliable and innovative manufacturer. The company reported a revenue of approximately $3.8 billion in 2023, reflecting its strong market position.
Dechang-motor’s commitment to research and development has been a driving force behind its success. The company invests heavily in innovation to meet the evolving needs of its clients. Its motors are designed to deliver high performance, energy efficiency, and durability, making them ideal for demanding applications in the power tools industry. This focus on quality and innovation ensures that Dechang-motor remains competitive in a rapidly changing market.
Note: Dechang-motor’s strategic partnerships and focus on innovation have positioned it as a leader in the motor manufacturing sector. Its ability to adapt to market demands and maintain high standards of quality underscores its importance in the global power tools supply chain.
Hardware Manufacturers

WeiDagroups 山东威达
WeiDagroups, established in 1976, is a leading manufacturer of precision hardware components. The company’s expertise spans a wide range of products, including drill chucks, CNC machine tools, robotic automation systems, and precision casting parts. Its comprehensive product lineup also features saw blades, powder metallurgy components, and switches for power tools.
The company has played a pivotal role in supporting the global power tools industry. Its drill chucks, known for their precision and durability, are widely used in electric drills and other power tools. WeiDagroups’ commitment to quality and innovation has earned it a strong reputation among international clients.
In 2023, WeiDagroups reported a revenue of approximately $3.3 billion. This achievement reflects its ability to adapt to changing market conditions and maintain a competitive edge. The company has invested in advanced manufacturing technologies, such as robotic automation and CNC machining, to enhance production efficiency and product quality.
WeiDagroups has also embraced sustainability in its operations. It uses eco-friendly materials and processes to minimize its environmental impact. This commitment to sustainability aligns with the growing demand for environmentally responsible manufacturing practices in the power tools industry.
Tip: WeiDagroups’ focus on precision, innovation, and sustainability makes it a vital contributor to the global power tools supply chain. Its ability to deliver high-quality hardware components ensures its continued relevance in a competitive market.
Impact on Power Tools Supply Chains

Disruption of Traditional Supply Chains
Decline in China’s manufacturing dominance
China’s dominance in global manufacturing has faced significant challenges in recent years. The imposition of tariffs, rising labor costs, and geopolitical tensions have prompted many companies to reconsider their reliance on Chinese production. Manufacturing’s share of total employment in China has declined sharply, mirroring global trends. For instance:
- Manufacturing’s share of total employment globally fell from 32% in 1955 to 8% in 2019.
- In Germany, manufacturing jobs dropped by 24 percentage points between 1973 and 2012, while the UK saw a 19-point decline during the same period.
These shifts highlight the broader trend of reduced dependence on traditional manufacturing hubs. Companies are diversifying their operations to mitigate risks and adapt to changing economic landscapes.
Increased costs and delays in sourcing
Tariff policies have significantly increased the cost of sourcing components and finished goods. Higher import duties on key products, such as cordless drills and battery packs, have forced manufacturers to absorb additional expenses or pass them on to consumers. This has disrupted supply chains, leading to delays and inefficiencies. Businesses now face longer lead times and higher transportation costs, further complicating their operations. The need for alternative sourcing strategies has become critical to maintaining competitiveness in the power tools industry.
Relocation of Manufacturing
Southeast Asia as a new hub
Southeast Asia has emerged as a preferred destination for manufacturing relocation. Countries like Vietnam and Thailand offer competitive advantages, including lower labor costs, favorable trade agreements, and strategic geographic locations. Vietnam, for example, has attracted significant foreign investment due to its robust infrastructure and government incentives. Thailand, with its skilled workforce and established industrial base, has also become a key player in the region.
The relocation trend is supported by statistical data:
Statistic Description | Value | Year |
---|---|---|
Mexico’s share of U.S. imports | 15% | 2023 |
China’s share of U.S. imports | 13% | 2023 |
Mexico’s foreign direct investment increase | 30% | 2022 |
Industrial property demand increase | 80% | 2023-2024 |
Manufacturing’s contribution to GDP | 17% | 2022 |

These figures underscore the growing importance of Southeast Asia as a manufacturing hub, driven by its ability to offer cost-effective solutions and access to emerging markets.
Mexico’s growing role in production
Mexico has solidified its position as a critical player in the global manufacturing landscape. Its proximity to the United States, the largest market for power tools, provides a strategic advantage. The United States-Mexico-Canada Agreement (USMCA) has further enhanced Mexico’s appeal by ensuring tariff-free access to North American markets.
In 2023, Mexico surpassed China in its share of U.S. imports, accounting for 15% compared to China’s 13%. This shift reflects the increasing preference for nearshoring to reduce transportation costs and improve supply chain resilience. Additionally, Mexico has experienced a 30% rise in foreign direct investment and an 80% increase in industrial property demand between 2023 and 2024. These trends highlight the country’s growing role in global production.
However, challenges remain. Scaling production to meet global demand and addressing infrastructure limitations require significant investment. Despite these hurdles, Mexico’s strategic location and trade agreements position it as a vital hub for the power tools industry.
Emerging Players in the Power Tools Supply Chain
Southeast Asia’s Role
Vietnam and Thailand’s advantages
Vietnam and Thailand have emerged as pivotal players in the global power tools supply chain. Vietnam’s strategic location near major shipping routes and its participation in multiple free trade agreements make it an attractive destination for manufacturers. The country also offers competitive labor costs, which are significantly lower than those in traditional manufacturing hubs like China. These factors have encouraged companies to establish production facilities in Vietnam, ensuring cost efficiency and streamlined logistics.
Thailand, on the other hand, boasts a well-established industrial base and robust infrastructure. Its skilled workforce and government incentives for foreign investors further enhance its appeal. Thailand’s proximity to other Southeast Asian markets provides manufacturers with easy access to a growing consumer base. The region’s dominance is underscored by its 35.77% share of the global power tools market in 2023, a figure expected to grow as industrialization and urbanization continue to accelerate.
Trade agreements and labor costs
Southeast Asia’s success is also tied to its favorable trade agreements. Vietnam’s participation in the Comprehensive and Progressive Agreement for Trans-Pacific Partnership (CPTPP) and Thailand’s free trade agreements with key global markets reduce tariff barriers, making exports more competitive. Additionally, the region’s labor costs remain among the lowest globally, allowing manufacturers to maintain profitability while offering competitive pricing. These advantages position Southeast Asia as a critical hub for the power tools industry.
Mexico’s Strategic Importance
Proximity to the U.S. market
Mexico’s geographical proximity to the United States provides a significant advantage for its manufacturing sector. The country benefits from reduced transportation costs and shorter delivery times, which are crucial for meeting the demands of the U.S. market, the largest consumer of power tools. The United States-Mexico-Canada Agreement (USMCA) further strengthens this relationship by ensuring tariff-free access to North American markets. Despite competition from China, Mexico’s manufacturing exports, particularly in electronics and transport equipment, remain vital. This proximity allows Mexico to maintain its competitiveness in the global power tools market.
Challenges in scaling production
While Mexico offers numerous advantages, it faces challenges in scaling production to meet global demand. Infrastructure limitations and the need for significant investment in manufacturing facilities pose hurdles. Additionally, the country must address workforce training to ensure a steady supply of skilled labor. Overcoming these challenges will be essential for Mexico to fully capitalize on its strategic location and solidify its role in the power tools supply chain.
Other Potential Markets
India and Eastern Europe
India and Eastern Europe are emerging as potential markets in the power tools supply chain. India, with its rapidly growing economy and large workforce, offers a significant opportunity for manufacturers. The country’s industrial sector is expanding, driven by government initiatives like “Make in India,” which aims to boost domestic manufacturing. Eastern Europe, particularly countries like Poland and Hungary, provides access to the European Union market and benefits from relatively low labor costs compared to Western Europe.
Infrastructure and policy hurdles
Despite their potential, India and Eastern Europe face challenges that could hinder their growth in the power tools industry. India’s infrastructure, including transportation and logistics networks, requires substantial improvement to support large-scale manufacturing. Policy hurdles, such as complex regulations and bureaucratic delays, also pose challenges. Eastern Europe, while benefiting from EU membership, must address political and economic instability in some regions. These factors highlight the need for targeted investments and policy reforms to unlock the full potential of these markets.
Note: The global power tools market, valued at USD 27.51 billion in 2023, is projected to grow to USD 40.20 billion by 2032. This growth underscores the importance of emerging players like Southeast Asia, Mexico, India, and Eastern Europe in shaping the industry’s future.
Business Adaptations to Tariff Policies
Diversifying Suppliers
Reducing reliance on single countries
Businesses are increasingly diversifying their supplier networks to reduce dependency on single countries. This strategy minimizes risks associated with geopolitical tensions and tariff fluctuations. Companies like Apple have shifted parts of their production from China to Vietnam and India. Similarly, Nike has expanded its manufacturing operations to Vietnam and Mexico, optimizing logistics and reducing costs. These moves highlight the growing importance of spreading production across multiple regions to ensure supply chain stability.
Building resilient supply chains
Building resilient supply chains has become a priority for companies navigating the complexities of global trade. Diversification of production hubs is a key approach. For example, an automotive manufacturer facing political instability with a primary supplier implemented a diversification strategy. This reduced production disruptions and improved overall supply chain resilience. By adopting similar measures, businesses in the power tools industry can better withstand external shocks and maintain operational efficiency.
Nearshoring and Regionalization
Benefits for North American companies
Nearshoring offers significant advantages for North American companies. By relocating production closer to home, businesses can reduce transportation costs and delivery times. Mexico, with its proximity to the United States, has become a preferred destination for nearshoring. The United States-Mexico-Canada Agreement (USMCA) further enhances this advantage by eliminating tariffs within the region. This approach not only improves supply chain efficiency but also strengthens relationships with local markets.
Examples of investments in Mexico and Southeast Asia
Investments in Mexico and Southeast Asia demonstrate the effectiveness of nearshoring and regionalization. Apple’s decision to expand production in Vietnam and India reflects a broader trend of diversifying manufacturing locations. In Mexico, foreign direct investment has surged, with companies establishing facilities to serve the North American market. These investments underscore the strategic importance of these regions in adapting to tariff policies and maintaining competitive advantages.
Investments in Emerging Markets
Establishing new manufacturing facilities
Emerging markets have become focal points for new manufacturing facilities. Companies are leveraging these regions to mitigate tariff impacts and access cost-effective labor. For instance, TENPOWER has invested $280 million in a Malaysian facility to produce cylindrical lithium batteries. This project, expected to begin operations in 2025, will enhance the company’s ability to support global clients in the power tools sector. Such initiatives highlight the role of emerging markets in reshaping global supply chains.
Collaborations with local suppliers
Collaborating with local suppliers is another strategy businesses use to adapt to tariff policies. Partnerships with regional suppliers help companies reduce costs and improve supply chain agility. In Southeast Asia, manufacturers are working closely with local partners to streamline operations and meet market demands. These collaborations not only strengthen regional supply chains but also foster innovation and growth in emerging markets.
Future Trends in the Power Tools Industry

Long-Term Effects of Tariffs
Continued diversification of supply chains
Tariff policies have encouraged businesses to diversify their supply chains. Companies are reducing reliance on single regions to mitigate risks associated with trade restrictions. This trend has led to the establishment of manufacturing hubs in Southeast Asia, Mexico, and other emerging markets. By spreading production across multiple locations, businesses can ensure operational continuity and adapt to fluctuating trade policies. This approach also enhances supply chain resilience, allowing companies to respond more effectively to global disruptions.
Growth of regional trade agreements
Regional trade agreements are playing a pivotal role in shaping the future of global manufacturing. Agreements like the Comprehensive and Progressive Agreement for Trans-Pacific Partnership (CPTPP) and the United States-Mexico-Canada Agreement (USMCA) have reduced trade barriers and fostered economic collaboration. These agreements provide manufacturers with tariff-free access to key markets, enabling them to maintain competitive pricing. As more countries join such agreements, the global trade landscape will continue to evolve, benefiting industries like power tools.
Technological Innovations
Automation and digitalization in supply chains
Automation and digitalization are transforming supply chain operations. Advanced technologies, such as robotics and artificial intelligence, are streamlining production processes and improving efficiency. Automated systems reduce human error and enhance precision, particularly in the assembly of complex components. Digital tools, including inventory management software and real-time tracking systems, provide manufacturers with greater visibility into their operations. These innovations enable companies to optimize workflows and meet market demands more effectively.
Data analytics for optimization
Data analytics is becoming a cornerstone of modern supply chain management. By analyzing large datasets, businesses can identify inefficiencies and implement targeted improvements. Predictive analytics helps manufacturers forecast demand, reducing overproduction and inventory costs. Additionally, data-driven insights support decision-making, allowing companies to allocate resources more effectively. This approach not only enhances operational efficiency but also strengthens the overall competitiveness of the power tools industry.
Sustainability and Ethical Sourcing
Importance of ESG in supply chains
Environmental, Social, and Governance (ESG) practices are gaining prominence in supply chain management. Companies are adopting ESG frameworks to align with global sustainability goals and meet consumer expectations. Research involving 792 companies in environmentally impactful industries revealed a positive correlation between ESG scores and financial performance. Firms with robust ESG systems reported higher returns on equity and assets, demonstrating the long-term benefits of sustainable practices. These findings highlight the importance of integrating ESG principles into supply chain strategies.
Aspect | Findings |
---|---|
Dataset | 2,376 observations from 792 listed companies in environmentally impactful industries (2019-2021) |
Analysis Method | Multiple regression techniques |
ESG Scores and Performance | Significant positive relationship with Return on Equity (ROE) and Return on Assets (ROA) |
ESG Dimensions Impact | All three dimensions (E, S, G) positively impact corporate performance |
Additional Factors | Company size and growth rate positively correlated; leverage ratio negatively correlated |
Case Study | Hunan Valin Steel Co., Ltd. reinforces findings |
Conclusion | ESG systems enhance financial performance and support sustainable development in impactful industries |
Pressure for sustainable practices
The demand for sustainable practices is reshaping the manufacturing landscape. Consumers and regulatory bodies are pressuring companies to adopt eco-friendly materials and reduce carbon emissions. Manufacturers are responding by investing in renewable energy sources and implementing waste reduction programs. These efforts not only address environmental concerns but also enhance brand reputation. As sustainability becomes a key differentiator, companies that prioritize ethical sourcing and green practices will gain a competitive edge in the global market.
Introduce CISIVIS TOOLS Brands
CISIVIS TOOLS has established itself as a global leader in the power tools industry, renowned for its innovation, quality, and customer-centric approach. With over 15 years of experience in the European and American markets, the brand has consistently delivered cutting-edge solutions tailored to meet the evolving needs of professionals and DIY enthusiasts alike.
A Comprehensive Product Portfolio
CISIVIS offers an extensive range of tools and accessories, encompassing nine distinct categories and over 3,000 products. These include:
- Power Tools: High-performance drills, saws, and grinders designed for demanding applications in construction, renovation, and manufacturing.
- Hand Tools: Ergonomically designed tools crafted from high-strength alloy steel for durability and user comfort.
- Measuring Tools: Precision instruments such as laser distance meters and electronic levels, ideal for engineering and mechanical tasks.
- Safety Equipment: Protective gear, including gloves, goggles, and helmets, ensuring user safety during operations.
- Tool Accessories: A wide array of compatible components like drill bits and saw blades to enhance tool efficiency and longevity.
Note: CISIVIS products undergo rigorous testing to meet international quality standards, including CE, VPA, and Energy Star certifications.
Global Manufacturing and Distribution Network
CISIVIS operates 12 state-of-the-art manufacturing facilities worldwide, with a strong presence in China, the United States, and Europe. These facilities utilize advanced automation systems, such as CNC machining and laser cutting, to ensure precision and efficiency. The company also maintains over 100,000 square meters of warehouse space, equipped with automated storage systems for rapid order fulfillment.
Region | Key Facilities and Warehouses |
---|---|
China | Wuhan and Nantong manufacturing bases |
United States | Warehouses in California and New Jersey |
Europe | Distribution centers in the UK and Germany |
Commitment to Innovation and Sustainability
CISIVIS invests heavily in research and development, with five R&D centers employing over 200 engineers. The brand introduces more than 400 new products annually and holds over 700 international patents. Recent innovations include AI-powered tools, renewable energy-driven devices, and eco-friendly materials, reflecting its dedication to sustainability.
CISIVIS also prioritizes ethical sourcing and green manufacturing practices. The company uses recyclable materials and energy-efficient processes to minimize environmental impact. These efforts align with global trends toward sustainability and responsible production.
Tailored Solutions for Diverse Needs
CISIVIS excels in providing customized solutions through its OEM and ODM services. Businesses can collaborate with the brand to design tools that meet specific requirements, from logo customization to unique functionality enhancements. This flexibility has made CISIVIS a preferred partner for enterprises seeking to differentiate their offerings in competitive markets.
Tip: CISIVIS’s ability to combine innovation, quality, and customization ensures its continued leadership in the power tools industry.
CISIVIS TOOLS remains committed to empowering users with reliable, efficient, and sustainable solutions. Its global reach, technological advancements, and customer-focused approach position it as a trailblazer in the ever-evolving power tools market.
Tariff policies have transformed the global power tools supply chain, presenting both obstacles and opportunities for manufacturers. Emerging markets like Southeast Asia and Mexico have gained prominence as production hubs, driven by competitive labor costs and strategic trade agreements. U.S. manufacturing output declined by 3.3% after tariffs expanded in 2018, while Mexico surpassed China as the largest source of imports into the U.S., according to the U.S. Census Bureau. These shifts underscore the industry’s need for diversification and nearshoring strategies to navigate evolving trade dynamics. Future advancements in technology and sustainability will further shape the industry’s trajectory, ensuring resilience and innovation in a rapidly changing global landscape.
FAQ
What are tariff policies, and how do they affect the power tools industry?
Tariff policies impose taxes on imported goods, influencing costs and trade dynamics. In the power tools industry, tariffs increase production expenses, disrupt supply chains, and encourage manufacturers to relocate operations to regions with lower tariffs and competitive labor costs.
Why are manufacturers moving to Southeast Asia and Mexico?
Manufacturers prefer Southeast Asia and Mexico due to lower labor costs, favorable trade agreements, and proximity to key markets. These regions offer cost-effective production and reduced tariff burdens, making them attractive alternatives to traditional manufacturing hubs like China.
How do tariffs impact consumers?
Tariffs raise the cost of imported goods, including power tools. Manufacturers often pass these additional expenses to consumers, leading to higher retail prices. This affects affordability and purchasing decisions for both professionals and DIY enthusiasts.
What role does sustainability play in the power tools supply chain?
Sustainability has become a priority in the power tools industry. Companies adopt eco-friendly materials, renewable energy, and waste reduction practices to meet consumer demand and regulatory requirements. These efforts enhance brand reputation and align with global environmental goals.
How are companies adapting to changing tariff policies?
Businesses diversify supply chains, invest in emerging markets, and collaborate with local suppliers to mitigate tariff impacts. Nearshoring and regionalization strategies also help reduce transportation costs and improve supply chain resilience.
What advantages do regional trade agreements offer manufacturers?
Regional trade agreements, such as the USMCA and CPTPP, eliminate or reduce tariffs, fostering economic collaboration. These agreements provide manufacturers with tariff-free access to key markets, enabling competitive pricing and streamlined trade operations.
Why is automation important in the power tools industry?
Automation enhances production efficiency and precision. It reduces human error, optimizes workflows, and lowers operational costs. Advanced technologies like robotics and AI also improve supply chain visibility, helping manufacturers meet market demands effectively.
What makes CISIVIS TOOLS a leader in the power tools market?
CISIVIS TOOLS excels through innovation, quality, and customer-centric solutions. Its extensive product portfolio, global manufacturing network, and commitment to sustainability position it as a trusted brand. Tailored OEM and ODM services further enhance its appeal to businesses worldwide.